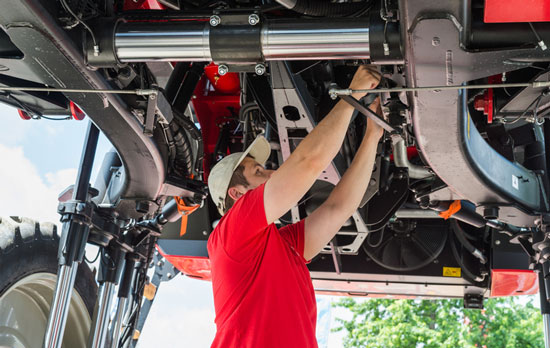
All News >> Digital Newsletters
Why Equipment Fails and How to Prevent It
December 28, 2020
Written By Zach Studer
No matter what industry you’re in, whether it be agriculture, construction, industrial, mining, forestry or transportation, you’ve undoubtedly had to deal with equipment failure. When equipment fails, it not only prevents you from completing your tasks but also comes with serious costs.
When we think about the costs of equipment failure, too often we only consider the cost to replace the damaged piece of machinery, but we fail to recognize the additional costs incurred. Equipment failure can lead to increased downtime, loss of productivity, increased labor costs, damage to personal property and, in some instances, personal injury or even loss of life.
Read the manual
One of the most common mistakes is also one of the simplest to avoid – not reading the owner’s manual. Technology is advancing rapidly and so are the lubricants that protect your machinery. Don’t make assumptions based on your previous experiences. Read the owner’s manual for all of your individual pieces of equipment to confirm the correct lubricant product, how often it should be changed or reapplied, suggested maintenance intervals, calibration instructions, and for troubleshooting information.
Make time for inspection
Insufficient lubrication is a leading cause of equipment failure. Too often heavy equipment operators are in such a hurry to get to work that they neglect to conduct routine inspections. Before starting any piece of equipment, remember to check the engine, transmission, gear box, coolant tank and other critical parts for proper fluid levels. Inspect fittings for sufficient grease coverage and apply as necessary. More than 40% of downtime in diesel-powered equipment is caused by cooling system issues, so be sure you’re using a fully formulated coolant like MFA Oil Extended Life 50/50 or Peak Final Charge Global 50/50.
Ensure operators are trained
Equipment operators can have a significant impact on the overall condition of your equipment. It’s important they are properly trained to use each piece of machinery and know the limitations of the equipment. When equipment is ran at or above designated maximum performance levels for extended periods of time, it can put extreme pressure on mechanical systems and lead to premature failure. Additionally, ask whoever is operating the equipment to report anything out of the ordinary. Strange smells, leaking fluids, delayed reactions, increase in vibrations or even a change in oil pressure or engine temperature are all potential warning signs.
Replace worn parts
If you see something that needs attention, fix it right away. It’s much easier to replace parts or to make repairs your equipment in the shop rather than in the field or on the road. While you’re at it, try to identify the source of the wear. Replacing a torn belt is only a temporary fix if the pulley is bad. Don’t ignore potential warning signals. Those lights on the dash are there for a reason.
Store it properly
Weather and exposure to the elements can play a role in breakdowns. Did you run that combine all day and put it away with only ¼ fuel left in the tank? If you did, you’re setting your equipment up for potential condensation issues that could lead to water in your fuel tank. Next time fill the fuel tank up before putting it away for the day. A full fuel tank greatly reduces the risk of condensation.
Be mindful of fuel storage
Starting with high-quality fuel is important but maintaining your fuel quality while its being stored is equally crucial. Regularly check your bulk fuel tanks for moisture and drain off any water at least twice per year. Fuel filters should also be changed two times a year (daylight savings adjustments are a good reminder). We recommend a 10-micron filter or smaller on bulk dispensers. When possible transfer your fuel directly from your bulk storage tanks into the equipment. If you must transfer it into a container first, ensure the container is clean and dry.
Analyze your fluids
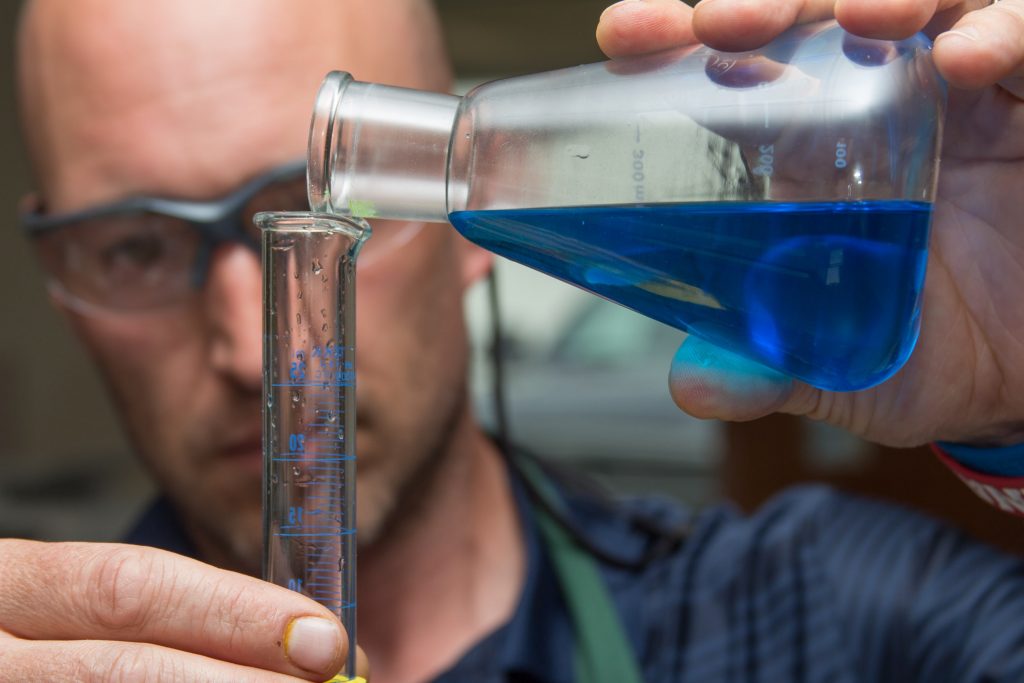
There are usually warnings signs that can be identified before equipment fails. The trick is to know what to look for. Oil analysis is an easy and cost-effective way to identify problems before they become severe. Think of it like going to the doctor and getting bloodwork done. You may feel normal, but there could be underlying signs of distress. Oil analysis is bloodwork for your equipment. It can reveal tiny wear particles and reveal which parts of your equipment are experiencing wear. Analysis can pick up on changes is viscosity, which indicates oxidation or fuel dilution, and it can also tell you if a lubricant is nearing the end of its life or if you can extend the drain interval.
While it’s nearly impossible to eliminate all breakdowns, you can avoid many of them by following a preventive maintenance program. That starts with putting the right products that meet the OEM’s specifications in your equipment. MFA Oil’s Work Horse product line has everything your equipment needs to stay in top running condition. Ask your local representative about our Oil Analysis Program. We will help you understand your equipment’s “bloodwork” and identify any underlying conditions before they lead to equipment failure. The MFA Oil Laboratory is available to answer any questions you may have about your fuel or lubricants.