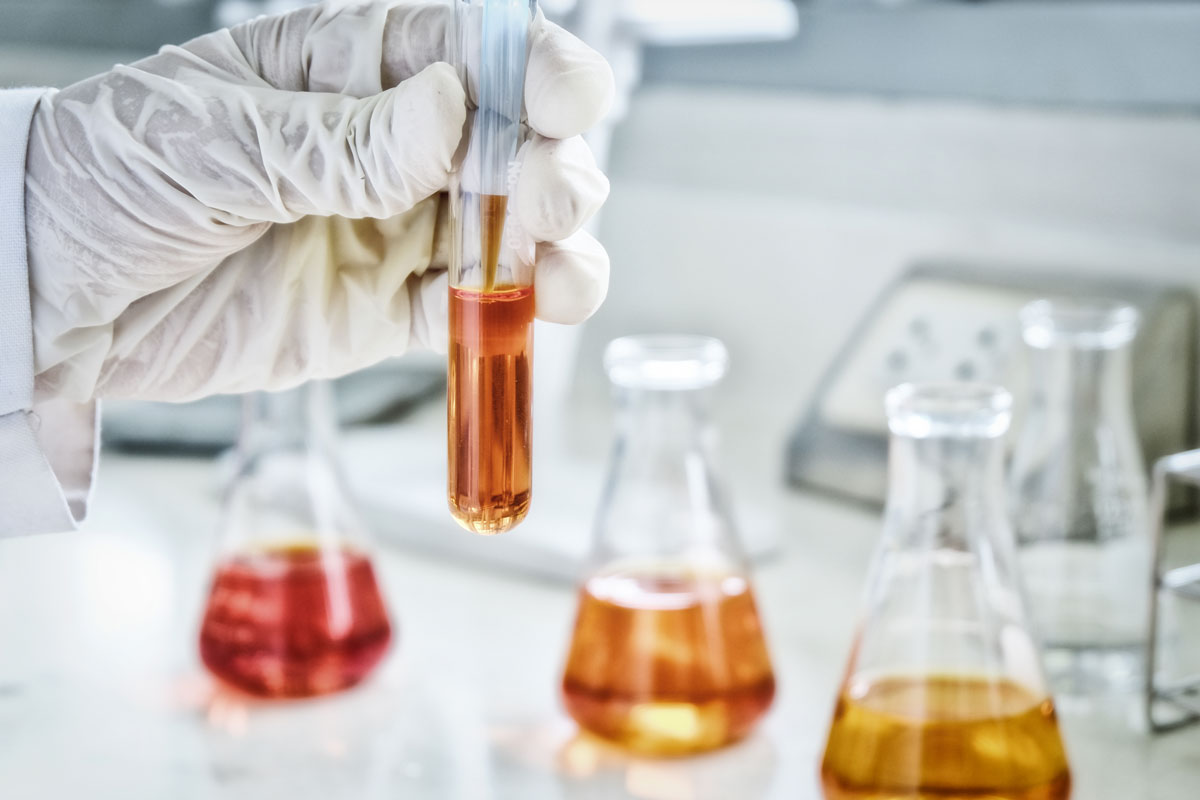
Lubricant Analysis Can Help You Avoid Costly Downtime
September 22, 2021
Written By Caitlyn Jolliffe
We’ll just run it until it breaks.” How many times have you heard this catchphrase? Equipment downtime is costly and often due to some form of contamination. The best way to guard against equipment failure caused by contaminants is to conduct regular lubricant analysis testing.
But testing alone is not enough. You also need to know what to do with the oil analysis results. This article will highlight the most common lubricant contaminants and provide tips on proactive and reactive maintenance that will keep your equipment up and running smoothly.
Abrasives
Abrasives such as dust, dirt, and other small particles can cause significant damage to your equipment. The naked eye can see some abrasives during a visual inspection, but that’s not always the case. Microscopic particles can be just as damaging if left unchecked.
Abrasives cause equipment to wear when the contaminants create friction between sliding, rolling, and thrusting parts. Abrasive contamination can damage gears, bearings, teeth, and other components while also lowering engine efficiency, restricting oil flow and part movement, increasing filter consumption, and reducing the lifespan of your lubricants.
Early detection of wear metals in lubricants and greases improves machinery reliability by helping you avoid expensive damage and downtime on high-value equipment. The best way to identify abrasive wear is to collect samples at every oil change and send them to the MFA Oil Laboratory for testing.
Wear metal and wear particle levels usually increase before machinery begins to exhibit symptoms, such as increased vibration, temperature changes, or unusual noise. We recommend conducting regular lubricant analysis and tracking the results. If you need help interpreting the lubricant analysis results, call the lab at 1-800-MFA-LUBE. These results give you a baseline to know the normal levels of metals you can expect to see. When metal particle levels increase above your benchmarks, you get an early warning against future problems. That’s when you know it’s time to inspect your equipment more closely and consider additional action.
If you see an increase in these metal particle levels, the best action to take is to change the oil and the oil filter. Make sure always to use new, quality lubricants and never use dirty containers to transfer new oils.
Water
Water is another common contaminant that can wreak havoc on your equipment. Lubricants with a hazy or milky appearance may be impaired by water emulsion, air, dyes, soot, or other contaminants. If a lubricant analysis confirms water to be the culprit, remove it as quickly as possible.
Equipment failures caused by water contamination can be devastating, but the damage is not always immediate. Rust, the most common result, occurs when water dissolves oxygen and oxidizes metal surfaces. Once metal oxidates, it begins to lose its physical integrity and becomes susceptible to failure. A bearing can lose 75% of its expected life due to water contamination before the oil even becomes cloudy.
The effects of water on your lubricants can be just as harmful:
- Water accelerates oil oxidation which degrades quality and robbing service life.
- It prematurely depletes oxidation inhibitors which protect against corrosion and sludge.
- Water causes some additives to precipitate, which causes them to attract additional contaminants and settle out or get caught by filters.
The best way to identify water contamination is by a visual test. Cloudy or milky-looking lubricants may have water contamination. However, trapped air can also create a hazy appearance in oil. Laboratory testing can confirm the presence of water in an oil sample.
Promptly removing excess water from a lubricant may help avoid severe damage to the fluid and lubricated components. One simple, cost-effective option is to drain settled water from the bottom of a lubricant system. This will remove any free water, but it is not effective against emulsified water or dissolved water. Other strategies include absorbent filters (good for minor water contamination), vacuum dehydration, and air stripping.
To reduce the likelihood of water contamination in the first place, consider the following:
- Store lubricants indoors in a clean, dry, temperature-controlled location when possible.
- If lubricants must be stored outdoors, use tarps and platforms to protect them from precipitation and groundwater.
- Check and replace any seals on equipment or stored lubricant containers that may be failing (or on the verge of failing) due to wear, swelling or other damage.
- Ensure caps, hatches and bungs on lubricant storage containers are tightly and securely closed.
- Prevent wash-down water from entering vents and reservoir covers.
- Install desiccant air breathers or vapor extractors.
Incorrect Lubricants
Cross contaminating your lubricant system with an incorrect product can cause several issues to your machinery and the lubricant itself. Your equipment may experience premature filter plugging, the buildup of deposits or varnish, worsening wear due to changes in additive concentration and loss of film strength.
Cross-contaminated lubricants could be damaged by oxidation, additive loss, viscosity changes, and loss of demulsifiers. These factors negatively affect the performance and life of lubricants and are a concern for both oils and greases.
In severe cases of incompatibility, even small amounts of incorrect fluid can cause big problems. The best way to diagnose improper lubricant application is to collect a sample from your equipment and send it to the MFA Oil lab for testing. If the results conclude the incorrect lubricant is in use, drain the fluid and refill with the correct product. If you need assistance with product recommendations, call the laboratory at 1-800-MFA-LUBE. The laboratory technicians can also advise of any potential incompatibility issues whenever you consider changing lubricant products.
Clear and proper labeling can help you prevent lubricant cross-contamination issues. Color coding containers and equipment application points with labels or tags is a proven strategy that works. The best label design incorporates a color or shape scheme for each lubricant used. This system offers a quick visual reference to show which oil or grease is in use. When possible, use a dedicated plastic container to transfer each lubricant to avoid contamination.
If you are proactive and take care of your equipment and it will take care of you.