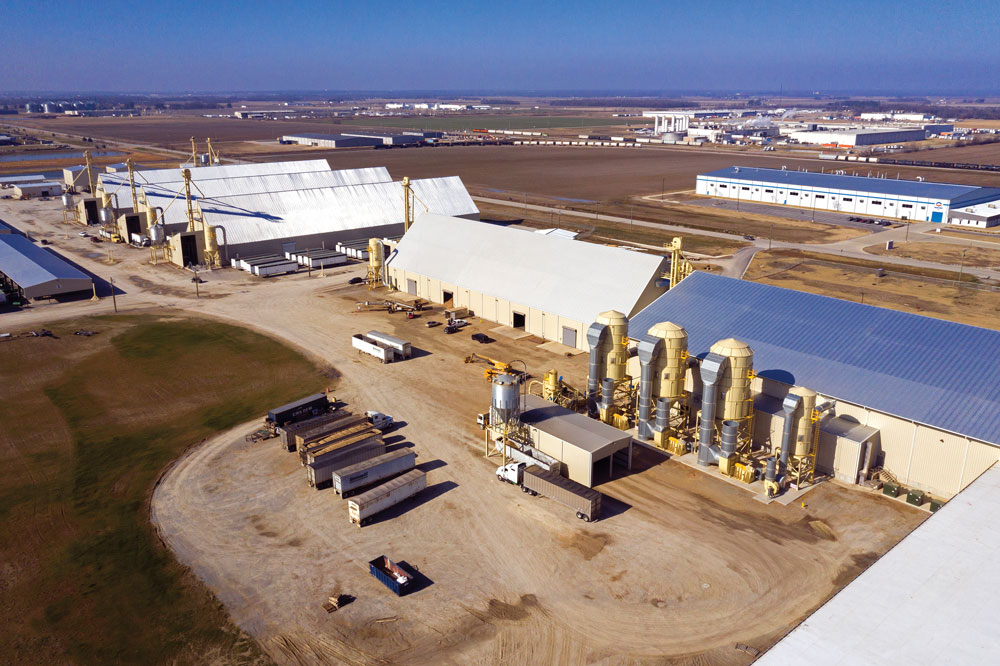
Building a Legume Legacy
March 2, 2021
Written By Jason Jenkins
Farmer-owned Peanut-shelling Facility Gives Growers More Control of Their Future
Most people wouldn’t be satisfied working for peanuts. Tommy Jumper came out of retirement to do just that.
After years of planning and development, Jumper and a group of farmer-investors opened Delta Peanut, the first peanut-shelling cooperative in Arkansas, in 2020. The $70 million, state-of-the-art facility sits on 71 acres on the east side of Jonesboro, serving as a hub for the region’s growing peanut industry.
“You can’t outrun the cost of freight,” says Jumper, CEO and managing partner for the farmer-owned co-op. “The companies that were buying peanuts here did so as risk mitigation against bad weather in other regions. However, shipping those peanuts to Georgia or Texas for shelling is expensive—more than $100 per ton. If we were ever going to grow our acres, there had to be a peanut-shelling plant here.”
Currently, 73 peanut growers representing nearly 50,000 irrigated acres in Arkansas, Louisiana and Missouri belong to the cooperative. Stronger together, their investment and vertical integration allows them to nearly double the value of their peanuts.
Growing goobers
Long considered a southern crop, peanuts today are commercially produced in 13 states: Alabama, Arkansas, Florida, Georgia, Louisiana, Missouri, Mississippi, North Carolina, New Mexico, Oklahoma, South Carolina, Texas and Virginia. Roughly half of the nation’s annual peanut crop is raised in Georgia.
There are four main types of peanuts: Virginia, Spanish, Valencia and runner. The Virginia type is large and best known to consumers as those sold in the shell at sporting events. The smaller Spanish type has a distinctive red skin and is prized for candy and confections, while Valencias are distinct because they produce three or more kernels per shell.
However, runner peanuts make up the vast majority of the U.S. crop, accounting for 85 percent or more of annual production. In fact, roughly 1.3 million acres of runners were planted in 2020. Thanks to a uniform kernel size, this peanut type roasts evenly, making it the perfect choice for producing consistent peanut butter. Consumers also will find these peanuts in candy bars, nut mixes or simply in a jar, roasted and salted.
Growing peanuts requires light, sandy soils and abundant irrigation—both of which can be found from the Missouri Bootheel through the Arkansas Delta and into northeastern Louisiana.
“Good cotton ground also makes good peanut ground,” says Vincent Kerperien, director of operations at Delta Peanut. “Like other legumes, peanuts fix nitrogen in the soil. Growers who put peanuts into rotation one year out of three with their cotton can see their cotton yields increase 200 to 400 pounds per acre.”
The peanut crop is planted in late April or early May using the same 38-inch row spacing as cotton. Unlike crops such as corn, cotton or soybeans, there are no herbicide-tolerant peanut varieties, so it’s important for growers to have a strong pre-emergent weed-control program. The growing cycle for peanuts in Missouri and Arkansas is relatively long, anywhere from 160 to 180 days, depending on the variety, Kerperien says.
“They may harvest a few in September, but the vast majority will be harvested through the month of October and into November,” he explains. “It’s a day-length-dependent crop, so every day you can leave it in the ground makes it that much more mature.”
Harvest is a labor-intensive process. First, a peanut digger pulled behind a tractor unearths the plants from the soil, gently inverting them so that the peanuts on the vine sit atop the rows with the leaf material below. Then, much like freshly cut hay, the peanuts are left to air dry.
“If weather conditions are good, the peanuts will be ready to combine after three to seven days,” Kerperien says. “Harvest is a slow process, sometimes as slow as 1 mph.”
Once the crop is dry, the combine picks up the peanut vines, feeding them into a threshing mechanism that separates the pods from the rest of the plant. The peanuts are transferred from the combine to a dump basket and eventually to a drying trailer, which is how the peanuts are transported from the field to the shelling facility.
“Our area is really fortunate,” Kerperien says. “Our growers are able to produce more tons per acre because it’s not been continuous peanuts. The last several years, Arkansas and Missouri have had some of the highest average yields in the United States, raising 4,500 to 5,000 pounds per acre.”
Coming out of their shell
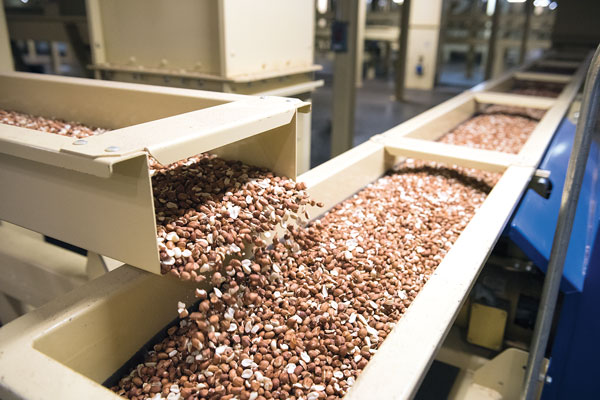
The harvested farmers’ stock peanuts are transported in drying trailers to Delta Peanut’s shelling facility in Jonesboro or one of the co-op’s buying points in Pocahontas or Marianna, Ark.
“Every load gets its own grade,” says Kerperien, noting that U.S. Department of Agriculture defines three levels of segregation for farmers’ stock peanuts based on damaged kernels and concealed damage. “Unless something catastrophic happens, most all peanuts end up in the top grade.”
The peanuts’ moisture level is determined. If the legumes are sufficiently dry, they are placed in the warehouse to await shelling. If they require more drying time, the entire trailer is moved to one of 100 drying stalls on site at the shelling facility.
“The trailers have a perforated false floor similar to a grain bin,” Kerperien explains. “We connect a duct to the front of the trailer and use propane-powered fans to blow warm air through the trailer until the peanuts reach the proper moisture.”
MFA Oil Co. supplies the facility’s propane. Jumper says the co-op has been a vital partner in getting the shelling operation up and running.
“We had enough other challenges, so we really needed somebody who’d say, ‘We’ll handle it,’” he says. “Our buddies at MFA Oil did just that. They took ownership of that piece of it, from estimating our needs to engineering the service to having conversations with the fire marshals. They’ve been really, really good to work with.”
Cured peanuts will remain in the warehouse until it’s time for shelling. When they enter the plant, the first step is rigorous cleaning to remove any foreign material.
“We use different-sized shaker screens and an aspirator that uses air to lift out debris. Anything heavy drops out of the flow,” Kerperien says. “We want only peanuts by the time they reach the sheller.”
Once the nuts are removed from their shells, they move through a series of machines that sort and size the peanuts for grading and packaging. Kerperien says the system is designed to extract the greatest amount of value from the legumes. “Every piece of the peanut is worth something, even that little nib piece between the two halves,” he adds.
USDA inspectors sample a peanut lot and determine its grade—jumbo, medium, No. 1, No. 2 or splits. The nuts are placed in 2,200-pounds bags, sealed and then moved to either dry storage or cold storage where they will remain until they are sold. The largest customers are Hormel Foods, which manufactures Skippy peanut butter in Little Rock, Ark.; the J.M. Smucker Co., which produces Jif peanut butter in Memphis, Tenn.; and the Algood Food Co., which co-packs peanut butter for private label brands in Louisville, Ky.
Jumper notes that the shelling facility is designed to process 25 tons of peanuts per hour. He estimates it will take about five years to reach capacity of 180,000 to 190,000 tons annually.
“That’s around 70,000 acres, so there’s still a lot of potential in this region,” he says.
Future peanut potential
While the Jonesboro shelling facility provides greater opportunity for peanut growers in the region, the co-op isn’t stopping there. Delta Peanut recently announced a new addition to its operations in Kennett, Mo., where both a blanching plant and seed-shelling plant will be constructed, along with another buying point.
“Some customers want peanuts with the skin still on the nuts. Some don’t, so those peanuts need to be blanched to remove the skins,” Jumper says. “There’s not any kind of blanching facility anywhere near us, so we can serve that market and add to our range of services.”
The seed-shelling plant will allow the co-op to clean seed for its members, as well as contract growers, without hampering operations at the main shelling plant. “We’re excited. The city of Kennett is excited,” Jumper adds.
As more growers consider adding peanuts to their portfolio, Jumper says there is room for more members in the cooperative. While he’s built businesses before, he says Delta Peanut and its stakeholders are different.
“So many businesses are built with an exit strategy, but this company has no exit strategy,” Jumper says. “We built this for farm families, families that will keep ownership of this business for generations, creating more wealth on the farm.
“We have a ‘why,’” he continues. “Many businesses know what they do, but they just don’t know why they do it. Well, we know our why, and we feel good about our why.”